If you take any interest to our products
Contact Us >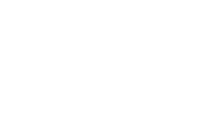
1. Filtration efficiency:
Conduct experiments to test the filtering efficiency of the filter cartridge, including its ability to capture particles and suspended solids of different sizes. A high-quality high-flow filter cartridge should have efficient filtering capabilities, effectively removing fine particles and impurities to meet the desired water quality standards.
2. Lifespan Evaluation:
Test the lifespan of the filter cartridge under actual conditions and observe its performance change during continuous operation. A high-quality high-flow filter cartridge should be able to operate consistently and stably for extended periods, reducing replacement frequency and maintenance costs.
3. Pressure Resistance Performance Testing:
Test the performance of the filter cartridge under certain water pressure and operating pressure. Max operating DP:2.4Bar (35psi) @20c.
4. Corrosion Resistance Assessment:
Test the filter cartridge's resistance to corrosion under specific conditions to determine if it can function properly in environments where it may come into contact with chemicals or acidic/alkaline substances.
5. Low-Pressure Drop Testing:
Test the water flow pressure loss generated by the filter cartridge under high flow conditions. A high-quality high-flow filter cartridge should be designed with a low-pressure drop to improve filtering efficiency and save energy.
6. Environmental Certification and Material Testing:
Check if the filter cartridge meets relevant environmental certification standards and if it is made with environmentally friendly materials. Ensure that the filter cartridge does not cause secondary pollution to the water quality.
7. Brand Reputation and Certification:
Understand the brand reputation and industry certifications of filter cartridge suppliers and choose products from manufacturers with a good reputation.
8. Customer Feedback and Reviews:
Collect feedback and reviews from other users regarding the filter cartridge to understand its performance in practical applications.
Based on the comprehensive testing and evaluation, you can select a filter cartridge product that is of high quality, has stable performance, and meets your requirements.
For any further questions or request detailed information, please reach us at sales@jielvfilter.com;
1. Polyethersulfone membrane (PES) filter element: It adopts PES membrane imported from Germany, with high hydrophilicity and low absolute accuracy of protein adsorption. Applicable for sterilization and filtration of aqueous liquids.
2. Polytetrafluoroethylene membrane (PTFE) filter element: divided into hydrophilic PTFE membrane, hydrophobic PTFE membrane, absolute precision, and wide chemical compatibility. Applicable for Gas sterilization and reduction of various acids, alkalis, and filtration of organic solvents.
3. Polyvinylidene fluoride membrane (PVDF) filter element: divided into hydrophilic PVDF membrane, hydrophobic PVDF membrane, absolute precision, and wide chemical capacity. Suitable for: gas sterilization filtration, and filtration of various acids, alkalis, and organic solvents.
4. Nylon membrane (N6N66) filter element: charged membrane, divided into N6 and N66 membranes, absolute accuracy. It is suitable for the filtration of organic solvents and sterilization of liquids.
5. Mixed cellulose membrane (MCE) filter element: hydrophilic membrane, low protein adsorption, absolute accuracy. Applicable: sterilization and filtration of aqueous liquids.
6. Polypropylene (pp) filter element: relative accuracy. Applicable for All liquid clarification filtration, pre-filtration, particle impurity filtration, and liquid precision filtration.
7. Glass fiber filter element: relative accuracy. Applicable for liquid pre-filtration, particle impurity filtration, and gas filtration.
8. Activated carbon fiber filter element: relative accuracy. Applicable for Liquid purification, deodorization, decolorization, and filtration of organic matter.
Contact Jielv Team ( sales@jielvfilter.com) for more information right away!
The filter cartridge is the core filter component of the liquid filter housing. Generally, the filter cartridges need to be replaced in time when they are deformed or damaged or when the liquid filter fails to meet the water outlet requirements.
Please refer to the replacement steps as follows:
1. Stop the filter and remove the manhole cover;
2. Unscrew the compression nut of the filter housing, remove the pressure plate, take out the filter cartridge, and then rinse the inside of the equipment with water;
3. Remove the upper and lower positioning rings at both ends of the filter cartridge, clean it with water, and then insert the two ends of the new filter cartridge respectively. It should be noted that before any new filter cartridges are used, they must be soaked for about half an hour to keep they are in a wet state;
4. Insert the end of the new filter cartridge with the lower positioning ring into the hole of the perforated plate;
5. Take the tie rod as the axis, put it into the pressure plate, insert the upper positioning ring of the filter cartridge into the corresponding pressure plate hole, and tighten the compression nut;
6. After the filter cartridge is installed, install the manhole cover and turn on the water;
7. Finally, open the water inlet valve and the exhaust valve. When the water is full of the equipment, open the clean valve, close the exhaust valve, and observe the water outlet from the clean outlet. After the water is free of foam, it can be put into normal operation.
It is recommended that you replace the filter cartridge when any of the following situations occurs:
1. The filter cartridge fails the integrity test;
2. The pressure difference reaches more than 2bar;
3. The flow rate does not meet the production requirements
4. Has reached a proven service life
5. The filter element is deformed or damaged;
6. When the filtration accuracy of the filter cartridge is reduced, the water effluent requirements cannot be met;
7. The water output of the system is not up to standard requirements,etc.
After production, thorough cleaning of the filter element can minimize the physical blockage of the filter membrane and is also a requirement for preservation or integrity testing of the filter element after production. For aqueous and organic solvent filter elements, the recommended cleaning methods are as follows:
1. Soak the filter element with 1% NaOH solution (30-60°C) for 2 hours, and wash it with pure water. However, Hybrid Cellulose Membrane Cartridges are not suitable.
2. Acid: soak the filter element in 0.5% HCI solution for 10 minutes, and rinse it with pure water.
Precautions
1. The filter element shall not be reversely flushed to prevent deformation under pressure;
2. Avoid being damaged by other objects during cleaning;
3. The filter element should be cleaned with high-quality water;
4. It is recommended that the general cleaning temperature be 30-60°C; the soaking cleaning time is 30-60 minutes;
5. After cleaning, the cleaning agent should be thoroughly washed;
6. If you want to use special cleaning agents or special cleaning conditions, please contact Jielv filter.
1. Characteristics of filter media
The filter membrane material is selected according to the characteristics of the liquid or gas. Generally, a hydrophilic membrane is used to filter an aqueous solution, and a hydrophobic membrane can be used to filter an organic solvent.
2. Filtered processing volume.
The filter size and the number of filter elements are considered according to the flux provided by the production process. Generally speaking, the flow rate of a 10-inch filter element is 0.5 ton/hour (the flux of filtered water). If the flux is to reach 1.0T, a 30-inch filter core can be selected, and some leeway can be reserved. The accumulation of impurities on the surface of the filter membrane will lead to a decrease in flux. If a filter with a core of 20 inches is used, it may not meet the requirements.
3. Pressure and temperature
The appropriate filter element is determined according to the filtration temperature, pressure, and disinfection conditions during filtration. The maximum working temperature of the general filter element is 80~90°C. Activated carbon fiber is 65°C, stainless steel folding is 200°C, and titanium sintered filter element can reach 280°C.
The maximum pressure of the microporous membrane folded filter element is 0.42Mpa/forward, the titanium sintered filter core is 0.5Mpa, and the stainless steel folded filter core is 0.6Mpa.
4. Excessive requirements
The degree of precision that filtration needs to achieve (requirements for sterilization and particle removal). The filtration efficiency of deep membrane filtration and absolute membrane filtration is different. For example, the absolute accuracy of 0.2um is basically used for sterilization; the relative accuracy of 10-20um can be selected for the removal of visible particles.
5, Filtering by step
According to the pollution degree of the filtrate and the impurity content, the pre-filter should be selected and the number of stages of filtration should be confirmed. The purpose of pre-filtering is to prolong the life of the final filter and reduce the cost. The design of the pre-filter affects the effect and life of the final filter.
By continuing to use the site you agree to our privacy policy Terms and Conditions.