If you take any interest to our products
Contact Us >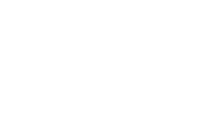
The filtration of food and beverages is also very important, which directly affects the health of subsequent human beings after consumption. It needs to be finely filtered through the water filtration system, which is strict to every process link.
Beer Filtration
Beer is made of malt and water as the main raw materials, adding hops, and fermented by yeast.
Main filter process and filter applications in beer production:
Gas filtration: Air particle removal sterilization filtration, carbon dioxide particle removal sterilization filtration, steam particle removal filtration.
Pre Filter: Polypropylene membrane filter with high dirt holding capacity.
Sterile filter: Polytetrafluoroethylene single-layer/double-layer filter membrane or 100% filter out various bacteria and bacteriophages, which can be repeatedly sterilized by online steam.
Steam filter: stainless steel powder sintered filter element, the absolute filtration accuracy in liquid is 10um and the filtration accuracy in steam is 1um.
Water filtration: Sterile water preparation and filtration system, used in tank area process water, yeast washing, CIP, Bottle washing machine, wine filling machine cleaning, etc.
Pre-filter and CIP filter are generally made of PP and other materials;
Sterile filter PES or Nylon and other materials;
The Filter cartridge is 100% integrity tested before delivery.
Wine filtration:
Ripe grape bunches are the most important raw material for wine making. craftsmanship is important for good wine. The brewing process tries to bring all the potential qualities that exist in the raw materials into an economical and perfect expression in the wine.
Filtration application in wine production:
1. Clarification filtration: Generally, use diatomite filter and cardboard filtration.
2. To remove acid salts (potassium tartrate, calcium tartrate) and other particles, PP melt blown or pleated filter element.
3. Recycling wine: Adopt solid-liquid separation system such as plate and frame filter press, etc.
4. Pre-filtering before bottling: PP or glass fiber pleated filter element.
5. Sterilization and filtration before bottling: PES/PVDF membrane filter element.
6. Process and bottle washing water filtration: PP High-flow pleated filter element, PP/ Glass fiber pleated/ Hydrophilic PVDF membrane/ PES Membrane filter element.
7. Sterile filtration in the process gases: Hydrophobic PTFE Membrane cartridges.
Packaged water filtration:
The packaged aquatic products on the market mainly include: drinking pure water, distilled water, drinking natural mineral water, drinking natural water, etc. The process of each product is slightly different, but they all have strict requirements on microorganisms, and new pseudomonas aeruginosa indicator. Water quality is critical.
For the filter cartridge that removes the microbial level, the bacterial challenge test must be carried out with international standard strains in accordance with international standard methods and procedures to determine the standard value of the integrity test of the filter cartridge in use, to ensure that the filter cartridge is completely trapped during final filtration. Pseudomonas aeruginosa and other harmful bacteria microorganism.
Main filtration process and recommended filter cartridge for bottled water process:
1. Coarse filtration and particle removal filter cartridge: application: water outlet, downstream of activated carbon, downstream of ion exchange resin.
2. Fine filter cartridge: suitable for mineral water/purified water, protect the final filter element, remove 0.5-2.0micron particles and other pollutants; reduce the number of microorganisms.
3. Security filter cartridge before RO reverse osmosis: pp melt blown, remove particulate matter, colloid and other impurities in water, and mee the requirement of reverse osmosis membrane water inlet SDI less than 5.
4. Final step filter cartridge: suitable for mineral water, purified water and other bottled water; remove microorganisms that cause water quality denaturation and are harmful to human body;
5. Pure water storage tank breathing port filter;
6. CIP Filter cartridge;
Soft Drink Filtration
The main raw materials of soft drinks are drinking water, extracts and concentrates of plant roots, steams, leaves, flowers and fruits, etc., and food additives such as sweeteners, sour agents, flavors, spices, food coloring stabilizers and preservatives are added. Some add a certain gas (such as nitrogen, carbon dioxide) to enrich the taste and product experience.
In the production process, the sterilization, particle impurity interception, and precise clarification involved in the process will have an impact on the final product quality, so it is very important to choose the appropriate filter product.
Main filtration process in soft drink production:
Water filtration: water for the product itself, water for CIP, water for equipment cleaning, water for aseptic filling, etc. Different applications have different requirements for filtering. PP melt blown/folded filter element is used for coarse filtration to remove large mechanical particles such as sand, activated carbon particle capture and filtration, ion exchange resin capture and filtration, and filtration before entering the clean water tank.
Water sterilization filtration: PES/Hydrophilic PVDF Membrane filter element, 0.22/0.45micron, verified by bacterial challenge test and integrity test.
Gas filtration (air, nitrogen, carbon dioxide, etc.): Pre-filtration of bas: used to remove particles and protect the sterilizing filter. Recommend PP pleated filter cartridge.
Tank ventilation and ventilation, sterile gas transmission materials, etc. Hydrophobic PTFE membrane filter cartridge is recommended, which can reach 0.01 micron when filtering gas. It has been verified by bacterial challenge test and can be tested for integrity.
Breathing port filtration of sterile storage tank: hydrophobic PTFE membrane filter cartridge is recommended, with a precision of 0.22 microns, which can reach 0.01 microns when filtering gas.
Filtration purpose of aeration filtration in liquid: removal of particles and high diffusion, high uniformity of aeration. The stainless-steel powder sintered filter cartridge is recommended, and can reach 1 micron when filter gas.
Dairy Filtration
Coarse filtration of raw milk, whey, skimmed milk. The purpose is to remove impurities such as large particles and protect the downstream process. Recommended products: filter bags, filter cartridges, stainless steel basket filters, etc.
Main filter steps and filter cartridge applied in production:p
1. Filtration of process water. Water outlet/downstream of activated carbon/ downstream of ion exchange resin for coarse filtration. Filters required: pp melt-blown filter cartridge, pp high-flow filter cartridge, etc. Capture/clarification filtration, protection of the final filter clement, pp pleated filter cartridge is required.
2. Sterilizing grade membrane filter, reduce or remove bacteria in water, recommend hydrophilic PVDF, PES membrane micron filter cartridge, etc.
3. Gas filtration. Process gas and ventilation sterilization filtration, pp pleated filtration cartridge is used for particle removal pre-filtration; sterilization filter element selects hydrophobic PTFE Membrane 0.22-micron filter cartridge.
4. The product is a high sterilization grade membrane filter to reduce or remove bacteria in water. Recommend hydrophilic PVDF, PES 0.65, 0.45, 0.22 micron filter cartridge.
5. Control of bacteriophages during dairy processing. Double-layer hydrophobic PTFE 0.22 micron membrane filter cartridge is recommended.
6. Filtration of functional ingredients added to dairy products, such as oligosaccharides, dietary fibers, minerals, etc. Recommend hydrophilic PVDF/ PES 0.65, 0.45, 0.22 micron filter cartridges.
7. Recovery of lye for CIP. Ceramic membrane filtration system or PP high flow melt blown filter cartridge, etc.
Other filtration aplications, such as ceramic membrane microfiltration technology for milk sterilization, ultrafiltration for milk protein concentration, nanofiltration for whey desalination, etc.
Juice filtration
Fruit juice is a fermentable but unfermented juice or slurry product made from fruits or vegetables by physical methods; or a juice that is recovered by adding the same amount of water removed during processing to concentrated fruit juice(slurry), slurry products.
The main filtration process in the production of fruit juice and its beverages:
Water filtration: Water for the product itself, water for CIP, water for equipment cleaning, water for aseptic filling, etc. Different applications have different requirements for filtering.
Coarse filtration is used to remove large mechanical particles such as sand particles, PP melt blown or PP pleated filter cartridge are used in this step.
Activated carbon particle capture and filtration, use PP melt blown or PP pleated filter cartridge;
Lon exchange resin capture and filter, PP melt blown or PP pleated filer cartridge;
Filtration before entering the clean water tank, pp Melt blown or PP pleated filter cartridge, Glass fiber filter cartridge;
Water sterilization filtration, PES/ Hydrophilic PVDF membrane filter cartridge, 0.22,0.45 micron, verified by bacterial challenge test and integrity test.
Gas filtration (Air, Nitrogen, Carbon Dioxide): Pre-filtration of the gas, protects the sterilizing filter, recommend PP pleated filter cartridge, 1 micron.
Tank ventilation sterile gas transmission materials, and sterile tank breathing port filtration, etc. Hydrophobic PTFE membrane filter cartridge is recommended, which can reach 0.01 micron when filtering gas. It can be verified by bacterial challenge test and can be tested for integrity.
Inflatable filtration in liquid: remove particles and high diffusion, high uniformity of inflation, recommend stainless steel powder sintered filter cartridge, filtering class up to 1 micron.
Steam filtration: steam for heat exchange equipment, steam for high temperature sterilization, steam directly in contact with food. Etc. A stainless steel powder sintered filter cartridge or a stainless-steel mesh filter cartridge is recommended, filter class up to 1 micron.
Fructose syrup filtration.
Main filtration steps and filter cartridge applications in the production of fructose syrup:
1. Steam filtration for jet heating: the saturated steam temperature is 107 °C, and mechanical impurities such as particles, rust, and welding slag are removed, which can ensure uniform steam jet and high dispersion. stainless steel powder sintered filter cartridge is applied in this filtration process.
2. Clarification of glucose syrup after saccharification: the temperature of sugar solution is 60-75°C, and the viscosity is 1-2CPS. It is necessary to remove impurities such as fiber, soluble protein, colloid, impurity polysaccharide, and submicron particles.
3. Decolorization and filtration: reduce the color of the product, improve the flavor, remove the peculiar smell, and make the product clear and transparent. The filter cartridge containing activated carbon can be used directly to achieve the effect of filtration and decolorization.
4. Finished syrup storage tank breathing port filter to ensure the cleanliness and microbial safety of syrup. Suggest stainless steel filter housing + Hydrophobic PTFE filter cartridge 0.22 micron.
5. Security filtration, temperature over than 60°C,viscosity varies from 10cps to hundreds of CPS. PP filter bags or filter cartridges are used to remove visible particulate impurities.
Edible oil filtration
Soybean oil, peanut oil and sesame oil are bulk oils, ad their fatty acid compositions are mainly oleic acid and linoleic acid, and they are the main edible oils for human beings. Generally, the free fatty acid content is less than 1%, and the quality of ordinary edible oil can be achieved after rough refining. However, it still contains a very small amount of impurities, and the impact of following impurities cannot be neglected.
Suspended impurities: sediment, embryo powder, cake residue, moisture;
Peptide impurities: phospholipids, proteins, sugars and low-level decomposition products,
Fat-soluble impurities: free fatty acids, diol, tocopherol, pigments, fatty alcohols, waxes;
Other impurities: toxins, pesticides.
Main filter process: In the edible oil refining process, a lot of activated carbon is used, acetone and clay are used as filter aids, decolorization, deodorization and precipitations, etc. These substances will inevitably flow into the downstream oil products. The high-efficiency filter bag has a filtration accuracy of 0.5 microns, which can collect these fine particles.
By continuing to use the site you agree to our privacy policy Terms and Conditions.