If you take any interest to our products
Contact Us >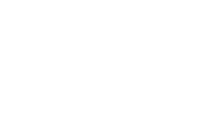
Filtration is such a widely used process in the pharmaceutical industry as to be considered almost omnipresent. Filtration can be easily applied to a large variety of pharmaceutical needs, and because of this flexibility, it is widely used within the industry.
Filtration and separation processes are not just important in the pharmaceutical industry, they are critical. Proper filtration makes sure that the products manufactured are safe for patients and ensures that manufacturers are not losing valuable products due to improperly working filtration processes.
Product safety is paramount in pharmaceutical production, which means that the highest quality standards have to be maintained. As a result, the filtration systems and filters that are used have to be effective in the filtration of aggressive fluids at multiple points in the process.
Surface filtration systems are designed for the purpose of retaining particles on the surface of the matter being filtered. These particles build up over time as filtration continues and form a solid layer of material on the surface level. This layer often referred to as a “cake layer,” helps increase the filter’s efficiency as it forms. While the initial rate of filtration when using surface filters is only around 55 percent, once a cake layer has formed, the rate of filtration increases to 100 percent. Within the surface filtration process, a reduction in flow will eventually occur as the matter continues to build up within the system, requiring occasional maintenance. The system will need to be stopped to allow for the filter to be cleaned.
Unlike surface filtration, depth filtration retains particulate matter farther down from the surface. It is primarily used for clarification of solutions. Among the most common filters used in depth filtration are ceramic-filtered and sintered filters. Recent developments in sintered metal filters: In the past, the industry depended heavily on using electrostatic precipitators, cyclones and disposable filters. But recently, these are being replaced by metal sintered filters. These filters can be cleaned in-situ, and as the filter cake (the layer of filtered material at the membrane) forms, the screen becomes more efficient.
The most typical example of cross-flow filtration is nanofiltration, a recently developed system for use by companies needing a method for dealing with low total dissolved solids water. The name nanofiltration comes from the use of a filtration membrane that has pores that are at or below one nanometer in diameter. It can be compared to reverse osmosis, but the trans-membrane pressure required for its operation is significantly smaller. The process is, therefore, more cost-effective. Despite this, it does have its shortfalls, as nanofiltration membranes may fall prey to fouling and scaling.
Another common type of filtration system used in the pharmaceutical industry is ultrafiltration. These systems are typically used when filter pores are required to be 0.01 micron in size. Ultrafiltration not only removes small particles from the flow of material, it also removes some viruses or other microorganisms that may be present in the flow, such as bacteria and protozoa. Materials that pass through the membrane of the filter are called “permeate materials,” while those that are held back and filtered out are called “retenate materials.”
Pharmaceutical processing facilities are all different, with unique filtration needs. Because processes vary and product safety is so important, manufacturers must consult with a reputable filtration company to make sure that they are receiving the right filters for their particular needs. For any more information about applications of filtration in the pharmaceutical industry, please do not hesitate to contact us.
By continuing to use the site you agree to our privacy policy Terms and Conditions.